Article • Opinion
The value of point-of-care
Some significant changes in the European hospital sector have occurred over the last 20 years. ‘The necessity to contain the exploding costs in particular has led to a reduction in the number of hospitals and hospital beds, and staffing levels have also been affected by the many cost cutting measures. This has not been without its consequences, as we now know,’ writes Ludwig F Rutten.
Whilst objects such as beds, medical devices or other materials may be easy to acquire, lease or hire, the situation is different when it comes to human resources. There is a lack of nurses, doctors, medical engineers and IT specialists, across the entire European employment market. Nothing damages a hospital’s reputation more than a rating that states it does not provide adequate patient care. There has been no getting away from it: Long waiting times and deteriorating care caused by a lack of staff on the wards are standard in many hospitals. This is particularly frustrating for all concerned when the respective budget is actually in place but suitable staff cannot be found.
There are obviously various ways to solve these problems. The easiest, but not necessarily most effective solution is to put the blame and responsibility on the ‘system’ and to wait until the system solves the problem. Actually, this tends to be the most common approach!
A much more successful line is to utilise improve productivity in existing resources more efficiently. A closer look at workflows repeatedly reveals a multitude of activities that originated in the past, but the necessity of which has never since been questioned.
One of the factors that could lead to a significant improvement in the situation is the handling of laboratory tests beyond the laboratory. A look at the entire process for some essential laboratory tests shows, without a doubt, that some tests could benefit from substantial improvements if the analysis was carried out on site, i.e. via a point-of-care test (POCT), rather than by a centralised service provider – the laboratory.
Some excellent examples of POCT can be found in the A&E department. Nowadays, to determine a troponin level via a POCT, within 15 minutes, is no longer a problem. However, the majority of A&E departments still send samples to the central laboratory. This results in long waiting times, unnecessary additional work for nurses and doctors and in patients spending far too much time in treatment rooms. What applied in the past is still relevant today: time is money. A solid analysis of the current situation and the willingness of all those involved to allow changes can lead to considerable increases in efficiency.
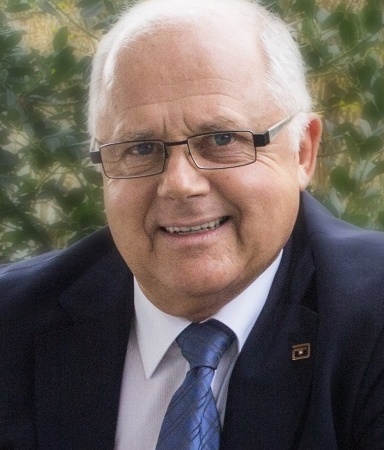
Naturally, it would be wrong to say that POC does not exist in European hospitals at all; it is already in practice in many places. The most important examples are blood glucose measuring systems and blood gas analysis. The question is, whether the right systems are being used. Finding systems that actually worsen a situation, instead of improving it, is not uncommon. Systems must fit into the workflow. In other words: When the decision is taken to establish POC, the optimum work process must be defined before the required systems are chosen.
Whether or not a POC concept supports workflows in a meaningful way depends to a large part on the performance of the IT systems used. Modern systems specifically developed for POC offer the user many opportunities to make working with the systems as easy and safe as possible. However, for this, an IT system that supports the different opportunities offered by POCT systems is a prerequisite. The latest systems make the use of pen and paper completely redundant. It makes no sense to make laboratory test results available more quickly if old, standard forms are then used to document patients’ results, or for the obligatory quality control documentation still required in some countries. A combination of ‘modern’ with ‘stone age’ would be counterproductive in this case.
What we would like to tell the observant reader with this contribution is that the integration of POC can only be successful if thorough preparation takes place beforehand. The change to POC is more than a discussion as to whether a system is technologically suitable to carry out certain types of analyses or not.
As the resulting profitability of a POC project directly depends on the increase in efficiency expected, all those involved should take enough time for a detailed analysis of the current situation and the results to be expected. If everything has been done properly POC will be the quiet force that helps to utilise the existing resources in the best possible way for a long time to come.
Profile:
Currently co-owner of POCTmedconsult GmbH, in Germany, Ludwig Rutten has more than 10 years’ experience in marketing Point of Care (POC) products. In a previous role, for example, he initiated several studies and workshops on process optimisation and POC.
06.11.2016