3D-Druck
Technologie mit Zukunft
Auf Basis anatomischer Daten werden im 3D-Druck-Verfahren patientenspezifische Implantate, anatomische Modelle, Schablonen und Bohrlehren hergestellt. Komplexe medizinische Eingriffe können damit besser geplant, vorbereitet und durchgeführt werden. Häufig initial von der Radiologie angefragt, profitieren vor allem die behandelnden Abteilungen. Der 3D-Druck von Biomaterialien zum langfristigen Verbleib im Körper ist aber noch Zukunftsmusik. Martin Herzmann ist Sales Manager DACH bei der Materialise GmbH, einem Unternehmen, das sich auf den 3D-Druck von anatomisch-medizinischen Anforderungen spezialisiert hat. Im Gespräch mit European Hospital zeigt er Potenziale und Herausforderungen dieser Technologie auf.
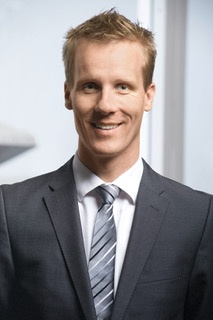
Service der Radiologie
MRT-, CT-und Ultraschall-Untersuchungen liefern die Datenbasis. Was weiter mit den Daten geschieht, klärt die Abfrage bei den eigentlichen Profiteuren des Verfahrens, den behandelnden Ärzten aus den Abteilungen Urologie, Kiefer-und Gesichtschirurgie, Neurochirurgie, Unfallchirurgie, Orthopädie und Kardiochirurgie. Als Serviceleistung der radiologischen Abteilung erfolgt dies über eine Checkbox: Sollen die Daten ins PACS-gespeichert werden? Möchte der Arzt die Daten im Ausdruck? Oder soll ein anatomisches Modell geliefert werden? Ein Häkchen genügt im Idealfall, wenn 3D-Druck erfolgreich in den klinischen Ablauf eingebettet ist.
Schablonen geben Führung
Die patientenindividuellen Schablonen werden aus biokompatiblem Kunststoff angefertigt und finden zum Beispiel in der Gesichtschirurgie Verwendung: Zur Rekonstruktion eines Unterkiefers wird häufig Knochen aus dem Wadenbein verwendet. Um passende Versatzstücke zu erhalten, werden Resektionsschablonen erstellt, die passgenau an Wadenbein und Kiefer auf den Knochen gesetzt werden. Sie definieren so die Schnittstellen und bieten zudem eine Führungshilfe für die chirurgische Säge.
Implantate sind tabu
Noch druckt keine Klinik ihre Implantate selber. Dies hat gute Gründe: Der 3D-Druck von Titan ist extrem komplex, die Anforderungen an die Räumlichkeiten sind kaum zu erfüllen und die Verarbeitung von Metall ist aufwendig. Außerdem gibt es eine haftungsrechtliche Problematik, in die sich eine Klinik mit selbst hergestellten Implantaten begibt. Daher ist für Implantate, die ja prinzipiell längerfristig im Körper des Patienten verweilen sollen, ein industrieller Fertigungsprozess vorgeschrieben.
Bioprinting noch visionär
Das Verfahren der Zukunft ist der 3D-Druck von lebenden Materialien, also Organen und Gefäßen. Zurzeit ist Bioprinting noch eine Vision, die in nur wenigen Zentren mit extrem hohem Aufwand in die Realität umgesetzt werden kann. „Wir sind in diesem Bereich selbst noch nicht engagiert“, so Herzmann, „aber wir liefern die Software.“ Genauer gesagt handelt es sich dabei um eine Analyse- und CAD-Software, die speziell für anatomische und physiologische Fragestellungen entwickelt wurde. Sie verfügt über anatomische Features, um zum Beispiel Volumina und Hohlräume zu messen oder den Knochenaufbau zu analysieren. Biomaterialien haben ganz andere Eigenschaften als anorganische Stoffe, wie Metalle und Kunststoffe. Sie sind weicher und flexibler. Dies muss beim Druckverfahren berücksichtigt werden. Bei Resektionsschablonen aus Kunststoff kommt das Lasersintering-Verfahren zum Einsatz. Dabei wird in einem Pulverbad punktuell und mikrometergenau Material schichtweise miteinander verschmolzen. Es entsteht ein fester, in sich homogener Monoblock. Aufgrund der hohen Temperaturen verbietet sich dieses Verfahren jedoch für die Verarbeitung von organischen Materialien. Alternativ wird beim Bioprinting daher das Material mit Druck auf einen spezifischen Punkt in einem Koordinatensystem gepresst. Zelle um Zelle wird so aufgetragen, die zusammen organische Layer ergeben. Im Idealfall sollten die Zellen nicht nur in ihrer jeweiligen Schicht miteinander kommunizieren, sondern auch innerhalb der verschiedenen Schichten interagieren können, wie in einem lebenden Organismus. „Das zu simulieren, zu gestalten und zu fabrizieren, ist ein hoch komplexer Vorgang“, erläutert Herzmann. „Bis zur Leber im 3D-Druck ist es daher noch ein weiter Weg.“
Viele Perspektiven
Ein weiteres für den 3D-Druck interessantes Material ist Magnesium. Es lässt sich mit Röntgenstrahlen gut durchleuchten und wird nach und nach vom Knochen absorbiert. Eine stabile Magnesiumschraube, die in einen Knochen eingebracht wurde, löst sich daher im Laufe der Zeit von selber auf. Magnesium in Pulverform ist für den 3D-Druck grundsätzlich geeignet, die Verarbeitung ist allerdings nicht ganz trivial. Für Herzmann ist Magnesium ein ideales Material für chirurgische Zwecke. Dennoch, die Strategie von Materialise sieht zur Zeit anders aus: „Die für den 3D-Druck etablierten Materialien wie Kunststoffe und Metalle bieten uns immer noch sehr viel betriebswirtschaftlichen Spielraum. Dieses Potenzial schöpfen wir zunächst aus, bevor wir uns innovativeren Richtungen à la Bioprinting für Kliniken widmen“, erläutert Herzmann. Einen Fokus stellt zurzeit die urologische Applikation dar. Haptisch echt und transparent gestaltet bieten urologische Modelle eine breite Anwendung: Zur Simulation patientenspezifischer Behandlungen und Operationen oder zur Darstellung anatomischer Situationen im Schulungsbereich etwa. „Langfristig sehen wir jedoch in der Radiologie mit ihrem breiten Spektrum für uns den Markt der Zukunft“, ist Herzmann überzeugt.
Profil: Martin Herzmann ist Sales and Marketing Manager Medical bei Materialise Deutschland und seit zwei Jahren speziell für den Bereich Medizintechnik, d.h. 3D-Druck und dazugehörige Software und Services für Firmen und Kliniken, verantwortlich. Zuvor war Herzmann acht Jahre bei Ziehm Imaging, im Marketing für intraoperative Röntgenbildgebung, nachdem er ebenfalls acht Jahre bei Brainlab mit Fokus auf intraoperative Navigation, Strahlentherapie und medizinische Software arbeitete. Er ist Mitglied des Regierungsprojektes "Nationaler Strategieprozess Medizintechnik" und Gründungsmitglied sowie Mitglied des Vorstandes des MedTech Circle e.V.
13.02.2017