Interview • Process optimisation
The Lean concept in digital pathology
We talked to Dr Annika Blank, Consultant and Lean green belt, about eight-year experience with the concept and optimisation of processes, the implementation of digital pathology and a voice recognition system for patient management.
Interview: Walter Depner
EH: In autumn 2014, Professor Alessandro Lugli reported on the first successful years the Lean concept use in pathology. Originally used in the automobile industry, this was designed to increase effectiveness, improve quality, processes, workflows and customer-orientation and much more. The system also impacts on the premises, staff (e.g. to avoid overtime), and added value. To what extent can you vouch for these improvements eight years on, and what else should be mentioned?
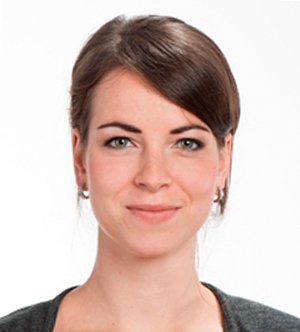
Annika Blank: The biggest and most cost intensive step taken to optimise workflows was the refurbishment of our laboratory, which was completed in 2016. This allowed us to adapt our premises to the workflow defined by the Lean principles. The design of the laboratory with individual work stations is now based on the processing steps for the samples. A very open-plan design has helped to make the path of the samples through the laboratory visible, to cut down on legwork and facilitate flexibility for innovations and communication.
The increase in value-added time has freed up more time resources for other responsibilities. This includes quality control and assurance, staff training and academic obligations, lectures and courses.
Measures implemented so far have been very successful with regards to processing times. Now we are at the point where we need to optimise the defined processes further to avoid stagnation. We are facing two major challenges: actively fighting against ‘operational blindness’ by constantly scrutinising ourselves and our processes, and redefining processes to make them as simple as possible. Finding simple solutions for problems and ensuring that they can be implemented with ease often poses a great challenge.
Pathology depends on cooperation with colleagues in many different departments/wards internally, as well as with those who send samples from outside the hospital. How has this cooperation developed in the context of Lean?
We see our task as simplifying the work of individual doctors
Annika Blank
One of the most important principles of Lean is the focus on the customer. The needs of the patient and of our clinical colleagues are at the centre of our work. We are constantly asking our senders for their opinions and suggestions for improvements through surveys and personal conversations, so that we can adapt our work to this as best possible. We see our task as simplifying the work of individual doctors.
One process where this was implemented successfully was the introduction of standardised reports for malignant tumours. The standardised reports make it easier to achieve a diagnosis as they contain all relevant information and contribute to the completeness of the diagnosis. The structure of the report has led to more clarity and comprehension. Monitoring our processing times makes the release of reports and their availability to those who send in the samples more predictable, which in turn makes it easier to plan the next appointments with patients to discuss the results.
Close cooperation with clinical colleagues is also very important for the quality of the diagnosis as the interpretation of the histological results often depends on the respective clinical context.
Recommended article
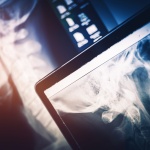
Article • Teleradiology
Integrate technologies to upgrade reports
As the demand for imaging studies booms and digital pathology takes off, it is becoming necessary to look at the interactions between radiology and pathology in telemedicine, an expert explained during the Radiology Triangle Madrid meeting early this year.
What impact has Lean had on the case numbers and staff numbers compared to 2011?
The number of staff members has increased by 7.5% since 2011, and the number of samples received has grown by 40%. The reduction of legwork, waiting times and unnecessary work stages results in more efficient handling, making it possible to process more samples in the same amount of time, without increasing the workload of individual staff members per time unit.
Digitisation of pathology has become an important topic over the last few years. One of the largest institutes in Switzerland, and one of the most important in Europe, must surely be part of this development. What progress have you made in Bern?
At our institute, we integrated digital pathology into the workflows step by step in those areas where we see its implementation creating added value. Digital pathology has been an integral part of our research projects since 2012. Scanned histological sections can be used in many ways. They facilitate access to sections for international cooperation, can be evaluated with the help of image analysis procedures or used as the basis of annotations to develop so-called tissue micro arrays.
Since 2016, we have been using an online platform to exchange information on certain cases with external assessors. Since 2017 this platform has also been used to display sections during case discussions with clinical colleagues and for tumour boards.
Cost-benefit considerations are of essential importance in daily, routine diagnostics. Digital pathology delivers added value for the evaluation of complex parameters, such as the proliferation fraction of tumours based on immunohistochemical markers. We are currently working on the development of robust algorithms for the evaluation of such parameters and will integrate these into diagnostic routine in spring 2019. Something that used to be laboriously counted by hand can now be analysed via automation, as long as it passes the pathologist’s plausibility check.
Recommended article
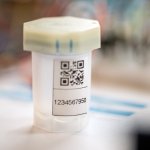
Article • Connected laboratory
Digitisation and automation: Game-changers in histopathology?
Often referred to as the ‘Achilles’ heel’ of histopathology, the sample entry has posed considerable challenges in pre-analytics for several decades. We visited the Munich-based lab automation start-up Inveox GmbH. Time-intense, highly manual processes in labs are expensive, error-prone and the most common reason for irregularities in cancer diagnoses. In Germany alone, every year hundreds…
Does the Lean concept impact digital pathology, and if so, how?
As digital pathology will soon become part of routine diagnostics, it is integrated into our workflow of laboratory processes and must adhere to the Lean principles to keep up with the pace of our case processing. Lean principles can not only be implemented in the design of workflows but will also be used for the appropriate utilisation of our resources and for quality control, particularly for quality of scans.
The institute’s annual report mentions that the introduction of voice recognition for the patient management system is an important component. How far have you progressed in this field?
The introduction of voice recognition in diagnostic routine was one of our main objectives for 2019, on a medical level. It was implemented in March and has proved itself for the drafting of short reports of findings. Voice recognition will continue to be adapted to our needs and requirements throughout the year until it is also suitable for complex reports of findings.
Profile:
Dr Annika Blank is Consultant at the Institute of Pathology at the University of Bern, Switzerland, where the Lean concept was introduced in 2011. Thus it became one of the first European pathology institutes to do so. Five years have now passed since a Lean audit in 2014, in which the institute scored very well. The period was used to gather considerable experience, to think about further innovations and continued improvements.
08.07.2019