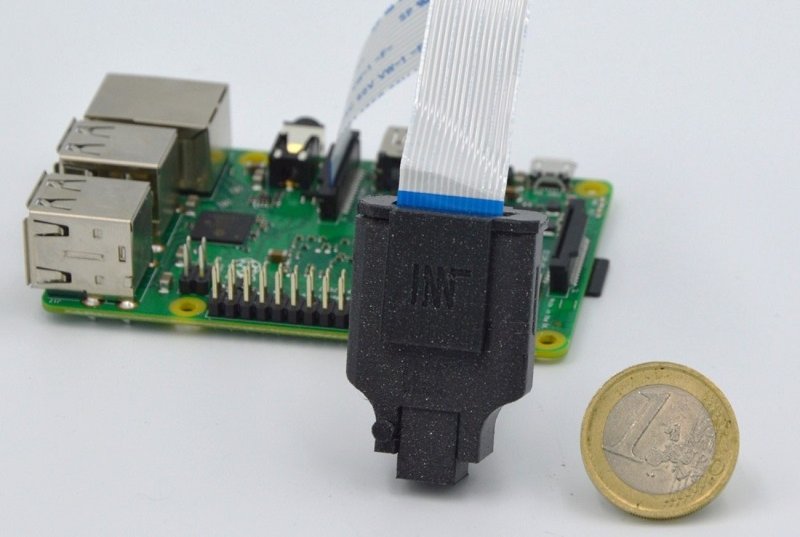
Source: Sophie Weiland
Article • Mini-microscopes
Are disposable robots conquering the labs of the future?
The team at the Institute of Medical Device Technology at the University of Stuttgart, Germany, is developing methods to produce top-quality medical devices at affordable prices. Professor Dr Peter Pott, the director of the institute, turns to 3D printers to successfully realize his vision of “high end at low cost”.
Report: Sonja Buske
“A great product is useless when it is so expensive that nobody can buy it,” says Pott, putting the dilemma in a nutshell. With production costs being of paramount importance, Pott and his team make parts and entire assemblies with 3D printers. “Particularly for small parts that are produced in small batches, 3D printing is much more cost-efficient than die casting”, he says.
One of the major advantages of 3D printing is the fact that the parts can be easily shaped into any form. “Nevertheless, there are certain limitations with regard to the achievable tolerances,” Pott, a mechanical engineer by training, concedes. “The components are not always identical in size and there is more deviation from the theoretical form than we are used from cutting. But even with imprecise parts we can build very precise systems.” The key concept here is tolerance management. Adjustments, reference edges und backlash allow the creation of a high-performing final product, as Pott knows from his many years of experience.
Fully automatic mini-microscope
Currently, Professor Pott is working on a miniaturized microscope made in a 3D printer. It will be able to process several samples in parallel and automatically. The small size is important since the device will have to fit in a small incubator.
“If, for example, active ingredient tests are performed on biological organisms, you need a lot of samples which ideally are being examined at the same time and under identical conditions,” says Pott. “Humidity, temperature or stability all play an important role. Sample handling has to meet complex requirements. That’s why we want to build a microscope that can work automatically in an incubator under uniform conditions without the samples having to be handled manually.”
Ideally, the data that is collected in this process is analysed with the help of artificial intelligence to save time and money. Pott adds: “The precision work of the 3D printer creates a miniature microscope with new functionality.”
Today, the mini-microscope is not mature enough to be deployed in the lab. “We need more money to speed up the work,” the director of the institute says but is optimistic that “the automation of microscope tasks will be an important aspect of biological research. There is no way we will be able to handle the high data volumes without this technology.”
Disposable robots
Rather more pie in the sky but equally interesting is another one of Pott’s projects: the disposable medical robot. “For many hospitals the use of robots is not profitable – they lose money,” Pott reports and adds that “the robots have many advantages, but they are still much too expensive.”
Thus he wants to produce robots cost-efficiently so the devices can be disposed of after use without qualms. “Reprocessing medical devices is a major cost issue. It is complex and binds resources. In addition, the devices have to be constructed in a way so they can be disassembled and they have to be made of materials that can withstand high temperatures and chemicals. With single-use devices this is no longer necessary which in turn makes production much simpler and cheaper,” Pott explains. Not to mention the added safety since there is no risk of pathogen contamination.
Pott is convinced that medical robots made of plastic are much cheaper to produce than robots that can be reprocessed. These devices would be much smaller and not durable. Initial tests at his Pott’s institute are very promising. And in this project as well, the 3D printer is the tool of choice. Some parts of the disposable robot are so small that they can be built only by 3D printers. In the final product, however, which will be manufactured in large batches, many components require die casting. But Pott is confident that he will achieve his ultimate goal: “I want to design a cheap and disposable medical robot for mass production.”
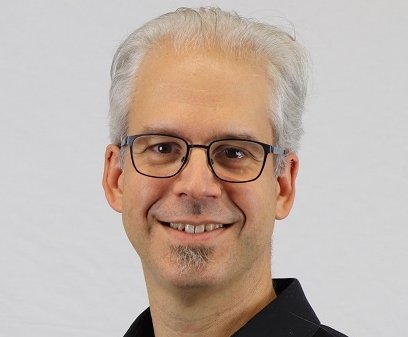
Profile:
Professor Dr Peter P Pott is head of the Institute of Medical Device Technology at the University of Stuttgart, Germany. After successful completion of mechanical engineering studies at the University of Applied Sciences in Mannheim and a subsequent supplementary programme at the University of Mannheim he worked at the Laboratory of Biomechanics and Experimental Orthopaedics of the University Hospital Mannheim.
In 2009, he joined the Institute for Electromechanical Design (EMK) at the Technical University Darmstadt where his research focused on medical technology and piezo actuation. In addition, he organised teaching and research at the institute.
In 2016, he briefly left the academic world to join Leica Microsystems CMS GmbH in Mannheim, but in 2017 he returned. Pott is a member of the Verband der Elektrotechnik, Elektronik und Informationstechnik (VDE) and other professional associations. In 2005, he received the Artur Fischer innovation Award and in 2008 the Walter Reis Innovation Award.
04.01.2022