Printing implants with the laser
Whether for individual micro-implants or for micro-implants with medicine depots – additive processes are ideally suited for manufacturing such components. In the project “REMEDIS”, scientists at the Laser Zentrum Hannover e.V. (LZH) have established a highly automated laser melting process to produce or coat implants made of platinum, nickel-titanium (NiTi) or stainless steel.
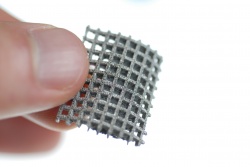
For this, scientists of the Surface Technology Group used a special form of 3-D printing – selective laser micro-melting (SLµM). They were able to coat electrodes for pacemakers with platinum, and produce three-dimensional lattice structures made of NiTi as well as stent prototypes made of stainless steel. Within this project platinum has been – for the first time successfully – processed within micro scale.
Coated pacemaker electrodes
One way to lengthen the life of pacemakers is to intelligently adapt the form and surface of the electrodes. Platinum has excellent electrical conductivity characteristics, and it is bioinert. However, the metal has casting limitations, and it is hard to be worked on in the micro-range using conventional methods. In the framework of this project, the scientists have developed an SLµM process for a platinum-iridium-alloy, and successfully coated implants.
Lattice structures made of shape memory alloys
The shape memory alloy NiTi is already widely used in medical technology. Micro-implants made of NiTi offer new possibilities for making tailor-made stents, or bone replacements for patients. The scientists at the LZH have been able to successfully manufacture highly-complex, three-dimensional component structures made of NiTi. A resolution of up to 90 µm has already been reached for components, retaining all of the characteristics of the shape memory alloy.
Stent structures made of stainless steel
The use of stainless steel 316 L for SLµM processes has already been established. Within this project, stent structures with a closed cell design have been developed and produced. Their mechanical characteristics are similar to those of conventional stents.
The project was carried out together with the Institute for Biomedical Technology of the University of Rostock, as a subproject in the cooperative project “REMEDIS”. REMEDIS was supported by the German Federal Ministry for Education and Research (BMBF).
Source: Laser Zentrum Hannover e.V.
21.07.2015