Article • Orthopaedic advances
Virtual training by hip implant simulator
Trainee trauma or orthopaedic surgeons have limited chances to practice hip replacement surgery before their first hands-on case. To change this, a team in the Dynamic HIPS project aim to improve this by creating a dynamic hip replacement simulator for future surgeons to practice the intervention and develop a reality-based feel for the procedure.
Report: Sascha Keutel
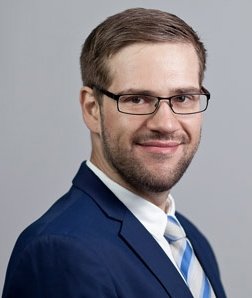
With an ageing population, the number of hip replacements is increasing – as is the demand for well-trained orthopaedic surgeons. The surgical procedure requires precision and physical strength. Currently, training junior surgeons depends on donor bodies and animals before the intervention can be performed in the OR supervised by an experienced colleague. ‘The use of virtual reality (VR) combined with haptic simulation would enable future surgeons to practice the intervention as often as necessary, without having to rely on donor bodies or animals and without having to put real patients at risk,’ according to Dr Mario Lorenz, research associate at the Institute for Machine Tools and Production Processes (IWP), at the Technical University (TU) Chemnitz. There, a simulator is being designed to complement current training methods and save scarce training resources.
Dynamic HIPS is the successor project of HIPS (HüftImplantatPfannenfräsSimulator), which was completed in 2019. ‘At the end of HIPS, we had developed a technically fully functioning system that could simulate milling the acetabulum and implanting the replacement hip with haptic feedback in virtual reality,’ Lorenz explained. But, he added, something was amiss. ‘The hard contact when placing the mill on the bone has to be generated by the robot within milliseconds to make the situation real for the surgeon.’ In the first clinical tests, however, the haptic feedback was outside the time range envisaged by the scientists.
Recommended article
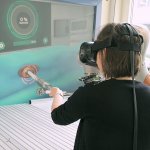
Article • Orthopaedics
VR training to improve hip replacement surgery
More than 200,000 patients undergo hip replacement surgery in Germany each year. To avoid complications and extend the lifespan of the artificial joint, the implants must be fitted precisely in the acetabulum (hip socket). The procedure, particularly milling the acetabulum, is not only difficult but also the technique is difficult to teach and train.
Project aims
This is how Dynamic HIPS was born, Lorenz explained. ‘We want to develop a haptic simulator that offers the surgeon the same sensory experience as real surgery. Above all, we want to map the forces at play when sawing or milling a bone.’ With the exception of opening the body and closing the wound, the researchers want to include all steps of hip replacement surgery in their expanded simulator – removing the femoral head with a bone saw, shaping the socket and placing the implant in the reshaped socket.
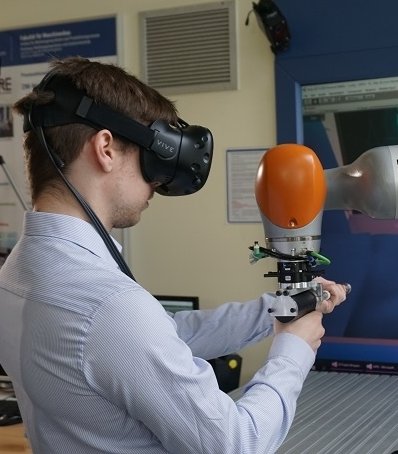
In a real operating room, the surgeon works on the femur and the acetabulum to fit the implant. In the virtual OR, the surgeon sees the virtual body and ‘feels’ it because the tools give mechanical feedback. The scientists want to identify the forces, torques and speeds that occur during each step of the procedure. On the basis of this data, they plan to develop a robotic arm and to further optimise current haptic tools.
First, the project partners create a mathematical model that more precisely simulates the resistance and the bone tissues removal. Furthermore, the team aims to develop a virtual OR where the trainee surgeon is supervised by an experienced senior physician. Such a remote training session could be performed across long distances and would facilitate knowledge transfer to newly developed and developing countries. ‘We want a collaborative multi-user system,’ Lorenz said. To this end, the project partners are developing a mathematical model that simulates the resistance and material removal on the bone even more precisely.
Due to travel restrictions caused by the Covid-19 pandemic, material tests had to be postponed to autumn 2021. Nevertheless, the project partners could finish all individual components. ‘We expect to be able to join all the components, that is to completely finish our extended prototype, by spring 2022,’ he said.
The project partners
In addition to the Chemnitz University of Technology, the University of Bremen and several companies are involved in the project. FAKT Software GmbH will integrate the components and build the training system, as well as the multi-user system. CAT Production GmbH developed the 3-D models of patient anatomy and of the OR. Haption GmbH will contribute an enhanced haptic systems and a module for user safety. YOUSE GmbH will ensure the user-centred approach of the project and monitor the ethical, legal and social implications (ELSI) of Dynamic HIPS.
The medical experts on the project are the Department of Orthopaedic, Trauma and Plastic Surgery at the University Hospital Leipzig, the Centre for the Study of the Musculoskeletal System (ZESBO), the Division of Macroscopic and Clinical Anatomy at the Medical University Graz (Austria) and the med-tech department of the Fraunhofer Institute for Machine Tools and Forming Technology (IWU).
The report was first published on www.tectales.com.
16.09.2021