Purchasing diagnostic systems
The acquisition of large diagnostic imaging equipment is clearly expensive – but further costs also result from their energy consumption and maintenance, as well as hidden costs due to complicated, labour-intensive handling, removal and disposal of old equipment, etc. often not considered during purchasing. Report: Anja Behringer
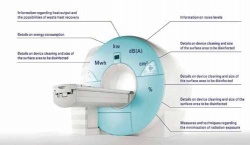
Making ecological aspects more transparent during acquisition and including these in the equipment calculations is the focus of a cooperation project for integrated product policies (IPP) in medical technology, initiated by the Office for Urban Development and the Environment in Hamburg. Hospital and clinic representatives in northern Germany, and those from companies such as Siemens, Philips, Agfa and GE Healthcare, and other German associations, e.g. the ZVEI (German Electrical and Electronics Manufacturers Association), linked up to establish which ecological criteria should be included in the evaluation of the use of medical devices.
From the project Ecological Product Information for Diagnostic Imaging Equipment a catalogue* of criteria, listing 27 points, was developed. The catalogue enables diagnostic imaging equipment buyers to ask manufacturers about the most important ecological criteria and therefore contribute towards a standard of information that ensures better comparison of important criteria for the environment and for purchasing budgets. The initiative is encouraging medical technology manufacturers to include the project results in their product descriptions. The advantages of the developed standards are obvious: Independent of the purchase price, hospitals and surgeries can identify potential savings in an environmentally friendly manner and, in the long term, be able to identify cheaper equipment. Along with a marketing gain, manufacturers will also gain insights into the customers’ expectations of the equipment, which may then influence product development.
Refurbished diagnostic equipment is also attractive to budget conscious healthcare providers. To ensure safe and fully functioning second hand equipment, COCIR (European Coordination Committee of the European Radiological, Electromedical and Healthcare IT Industry) developed its Green Paper on Good Refurbishment Practice. Among the members, Siemens has an advantage with its Proven Excellence Programme, which guarantees customers quality comparable with a new system at up to 30% lower purchasing cost. Around 90% of the materials of the initial products are used for refurbishment. Dr Freimut Schroeder of the Medical Solutions Environment, Health and Safety Division at Siemens in Erlangen, heads the Working Group Environment at COCIR. He emphasises: ‘Product-based environmental protection on the part of the EU must start during the product development phase. All diagnostic and imaging equipment in medicine should be supplied with comparable information about its environmental performance.’
In recent years Siemens’ refurbishment sites at Forchheim in Germany and HoffmanEstates in Illinois, USA, implemented the processes set out in the Green Paper. Positive reactions were also received from NEMA (National Electrical Manufacturers Association, USA), JIRA (Japan Industries Association of Radiological Systems), MIISC (Medical Imaging & Information Systems Council, Canada), the US Department of Commerce, and the Chinese Hospital Association. COCIR is now collecting feedback from all partners to develop the second version, which will form the basis for a future international standard. *English version: www.klima.hamburg.de/ ipp-medizintechnik
31.08.2011