Sponsored • Individuals for individuals
Printing 3-D human parts
Everyone is unique – and so is human anatomy. Thus orthopaedics or implantology call for medical products that provide a perfect fit and demand is high for one-off components, or small production runs. At the same time, the materials used and manufacturing standards applied must fulfil extremely stringent quality control. This also holds for specialised surgical instruments and medical devices, which must be produced quickly and cost-effectively.
‘EOS, the world’s leading technology supplier in the field of industrial 3-D printing of metals and polymers, enables exactly this,’ the company reports. ‘Based on 3-D CAD data, parts are built layer by layer, by depositing powder material instead of, for example, milling a workpiece from solid block by removing material. Where conventional manufacturing reaches its limits, industrial 3-D printing permits a design-driven manufacturing process allowing producers to come up with faster, more flexible and cost-effective development and production methods. Unlike conventional manufacturing methods, 3-D printing as such allows for maximum design flexibility and functional integration. Thus, test series, prototypes, patient-specific one-off parts and small production runs can be manufactured at a profit.
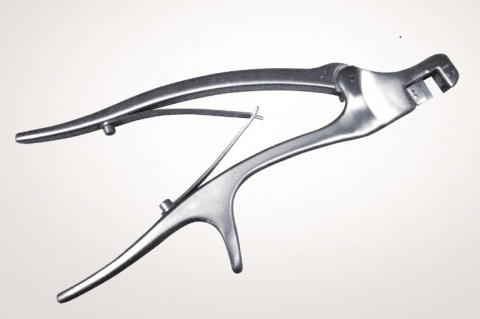
‘The medical sector recognised this and has been among the early adopting industries. Industrial 3D printing is meeting their requirements, supporting both surgeons and patients. Different patient populations around the world require different parameters for surgical equipment and medical implants. With additive manufacturing, patient-specific designs are possible, paving the way for an improved and “custom serial production” medical care. Orthopaedics adopted the approach very early on. So let’s take the example of a professional rock climber who experienced a complex fracture in his ankle that couldn’t be repaired.
Through medical scans, an exact replica of the climber’s ankle was reconstructed in a program that communicated a specific design to the EOS system. The 3-D printing technology was able to create a part that closely matched his anatomy and, once implanted, the climber’s recovery was quick because he had a more specific joint replacement rather than an ankle fusion or trauma plates that may not have allowed him to return to climbing. Beyond patient specificity, industrial 3-D printing also enables a greater complexity in surgical equipment design. EOS customer DePuy Spine had worked and partnered with leading clinicians and researchers for over 20 years to advance knowledge of both professionals and patients in addressing spinal pathologies and to develop products to treat spine disorders. Getting the right instruments to a surgeon who needs them can be an arduous process.
There’s still a long way ahead but it’s becoming more feasible
Eos
‘Prototyping, revisions, materials selection, cadaver testing and manufacturing can create total wait times of many months. DePuy Spine was able to cut those lead times dramatically by employing the EOS technology. DePuy Spine was able to introduce a paradigm shift in part design, as such not designing for manufacturability anymore, but for functionality. The consulting doctors now can be very exact about their requirements for tools such as blades, racks, tweezers, and callipers. CAD designs can be adjusted more easily and another duplication of a tool can be made – instead of just one – to give doctors more choice and greater flexibility.
‘Some opportunities the technology can offer are top in mind today: e.g. creating a point of care application, which is one of the many holy grails within the medical industry. Imagine being able to go to any hospital and have whatever ailment you had treated on the spot,’ Eos adds. ‘There’s still a long way ahead but it’s becoming more feasible while we continue to focus on material advancements and the continuing improvement of the technology.’
14.11.2017