Article • Integrated wiring
Clever cabling makes devices mobile
The integrated wiring of a medical device imposes great requirements on the cable system’s producer as well as the device manufacturer. This calls for a partnership collaboration particularly in development to ensure the system solution exerts a positive effect on mobility, user friendliness and robustness – long-term and reliably.
The integrated wiring of a medical device imposes great requirements on the cable system’s producer as well as the device manufacturer. This calls for a partnership collaboration particularly in development to ensure the system solution exerts a positive effect on mobility, user friendliness and robustness – long-term and reliably.
‘Qualified wiring is one of the success factors for large pieces of medical equipment,’ Leoni’s Healthcare Business Unit confirms. ‘Freedom of movement and user friendliness for staff, easy positioning and mobility for multifunctional use in, for example, hybrid operating rooms – the manufacturers’ requirements of the system technology are high.
‘Installed cables and cable systems must reliably withstand not only sometimes heavy tensile forces or repeated flexing but must also be fitted in such an efficient way that they do not obstruct any other components and allow short maintenance times. The reliability of the permanent transmission of data, signals, power, light and media is meanwhile essential.
‘Leoni’s Healthcare Business Unit meets the market’s challenges concerning innovative system solutions with more than 35 years of experience, know-how and a comprehensive portfolio. We can assist medical equipment manufacturers as early as the development phase of their device and provide input from the “cable’s perspective”.’
Clever cable routing facilitates flexibility
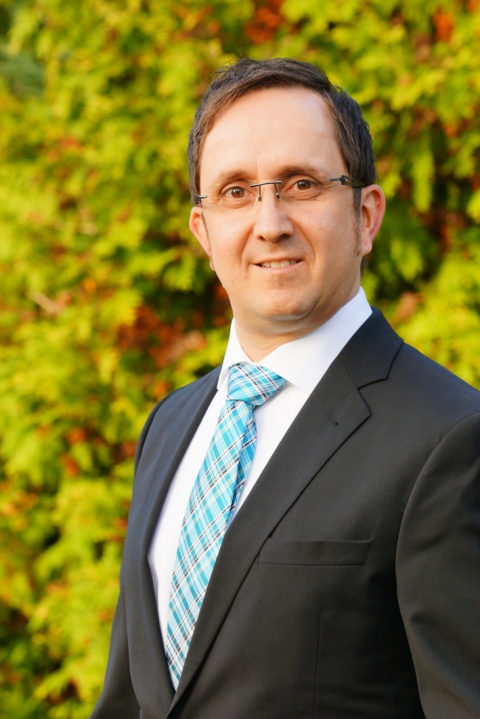
‘The key way to develop the wiring of a medical device involves optimally adapting the system technology and related cables to the movement sequences. That sounds easy, but it entails major challenges. Routing can cross rollers, sharp edges, joints or drag chains with the cables and components being pinched, rubbed, worn or dragged out.
‘To develop the specific system solution, Leoni’s engineers consider the movement sequences and speeds of the device or prototypes on the manufacturer’s site. Such early-stage involvement in the development process can yield innovative cable storage modules or spring return systems that reduce the mechanical forces on all components.
‘Spare cable length for long travel or high degrees of flex can be cleverly integrated in a device with innovative cable routing. In all cases the jacketing with an additional fabric, or other sleeve, ensures the desired robustness and that the system technology can be more easily disinfected.’
Less is often more
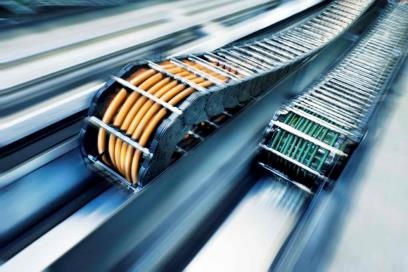
‘In addition to ready-to-connect system technology, Leoni can develop and produce application-optimised cables; such tailor-made cables can give the device manufacturer input on ways to save not only space, but also costs.
‘For example, because of the slower speeds involved, standardised drag chains are often a costly solution for medical equipment and do not even provide mobility in all directions. An application-optimised cable can be a more durable alternative.
‘In other cases, multifunctional and ready-to-connect hybrid cables can replace complex cable systems and simultaneously increase the mobility and robustness of a device.’
Leoni is at ECR 2018
Hall X1, Stand 139
Contacts:
tobias.hoeft@leoni.com
Phone: +49 4491 291 124 or +49 160-90192902
27.02.2018