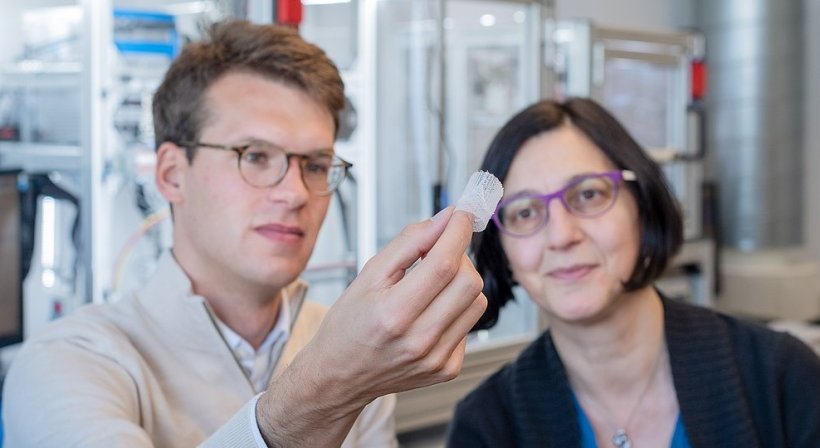
Image source: Andreas Heddergott / TUM
News • Novel manufacturing technique
3D printed heart valves to support tissue growth
Researchers have developed 3D printed artificial heart valves designed to allow a patient’s own cells to form new tissue.
To form these scaffolds using melt electrowriting – an advanced additive manufacturing technique – the team has created a new fabrication platform that enables them to combine different precise, customized patterns and hence to fine-tune the scaffold’s mechanical properties. Their long-term goal is to create implants for children that develop into new tissue and therefore last a lifetime.
The researchers published their findings on the novel valves and the manufacturing method behin it in the journals Advanced Functional Materials and Biomaterials Science.
In the human body, four heart valves ensure that blood flows in the correct direction. It is essential that heart valves open and close properly. To fulfil this function, heart valve tissue is heterogeneous, meaning that heart valves display different biomechanical properties within the same tissue.
A team of researchers working with Petra Mela, Professor of Medical Materials and Implants at the Technical University of Munich (TUM), and Professor Elena De-Juan Pardo from The University of Western Australia, have now, for the first time, imitated this heterogeneous structure using a 3D printing process called melt electrowriting. To do this, they have developed a platform that facilitates printing precise customized patterns and their combination, which enabled them to fine-tune different mechanical properties within the same scaffold.
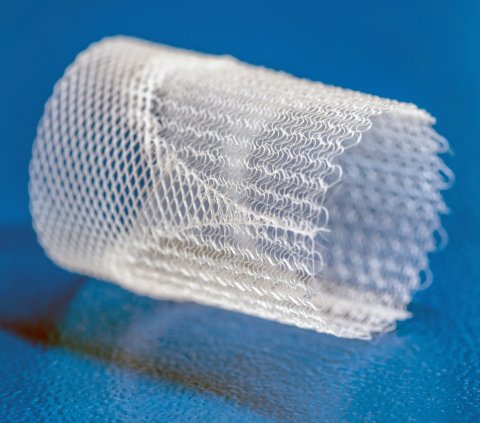
Image source: Andreas Heddergott / TUM
Melt electrowriting is a comparatively new additive manufacturing technology that uses high voltage to create accurate patterns of very thin polymer fibers. A polymer is heated, melted and pushed out of a printing head as a liquid jet to form the fibers. During this process, a high-voltage electric field is applied, which considerably narrows the diameter of the polymer jet by accelerating it and pulling it towards a collector. This results in a thin fiber with a diameter typically in the range of five to fifty micrometers. Moreover, the electric field stabilizes the polymer jet, which is important for creating defined, precise patterns.
The “writing” of the fiber jet according to predefined patterns is conducted using a computer-controlled moving collector. Similar to moving a slice of bread below a spoon dripping with honey, the moving platform collects the emerging fiber along a defined pathway. The user specifies this pathway by programming its coordinates. In order to considerably reduce the programming effort associated with the creation of complex structures for heart valves, the researchers developed a software to easily assign different patterns to different regions of the scaffold by choosing from a library of available patterns. Furthermore, geometrical specifications such as the length, diameter and thickness of the scaffold can easily be adjusted via the graphical interface.
Children would especially benefit from such a solution, as current heart valves do not grow with the patient and therefore have to be replaced over the years in multiple surgeries
Petra Mela
The team used medical grade polycaprolactone (PCL) for 3D printing, which is compatible with cells and biodegradable. The idea is that once the PCL-heart valves are implanted, the patient’s own cells will grow on the porous scaffold, as has been the case in first cell culture studies. The cells might then potentially form new tissue, before the PCL-scaffold degrades. The PCL-scaffold is embedded in an elastin-like material that imitates properties of natural elastin present in real heart valves and provides micro-pores smaller than the pores of the PCL structure. The aim is to leave enough space for the cells to settle, but to seal the valves adequately for blood flow. The engineered valves were tested using a mock flow circulatory system simulating physiological blood pressure and flow. The heart valves opened and closed correctly under the examined conditions.
The PCL-material was further evolved and evaluated together with Franz Schilling, Professor of Biomedical Magnetic Resonance, and Sonja Berensmeier, Professor of Bioseparation Engineering at TUM. By modifying PCL with ultrasmall superparamagnetic iron oxide nanoparticles, the researchers could visualize the scaffolds using magnetic resonance imaging (MRI). The modified material remains printable and compatible with cells. This might facilitate the translation of the technology to the clinics, as the scaffolds can thus be monitored upon implantation. “Our goal is to engineer bioinspired heart valves that support the formation of new functional tissue in patients. Children would especially benefit from such a solution, as current heart valves do not grow with the patient and therefore have to be replaced over the years in multiple surgeries. Our heart valves, in contrast, mimic the complexity of native heart valves and are designed to let a patient’s own cells infiltrate the scaffold”, says Petra Mela.
The next step on the way to the clinic will be pre-clinical studies in animal models. The team also works on further improving the technology and developing new biomaterials.
Source: Technical University of Munich
03.06.2022