Quality management in medical laboratories
Quality management (QM) for medical laboratories shaped its footprint during recent years – it’s a hot topic in papers, conferences and trade fairs. A lot of information makes a lot of work, says Dr Markus Neumann
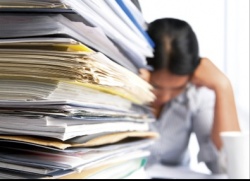
Although a bunch of IT products are available to help handle the numerous documents a laboratory must maintain (quality manual, quality system procedures, standard operations procedures), they normally lack the support of a special class of documents: a lot of information for reagents, supplied by the manufacturers for their analytical devices.
According to ISO 15189:2012: 4.2, 4.3, the lab must always control every document with content that could affect the quality of the laboratory outcome. As this is also valid for external documents, it is obvious that a lot of information supplied by manufacturers of analyser and reagents falls under this regulation. In terms of ISO 15189, controlling means that active documents must be authorised before use, identified (e.g. in a document register) and held available at the point of use. Furthermore, at the end of a document’s lifecycle it must be removed from the point of use and at least one copy has to be retained for a specified time.
While a laboratory normally offers more than a handful of analytical tests to customers (depending on size and specialisation of the lab there could be considerably up to a thousand tests) the extent of resulting external documents may become innumerable. Fortunately manufacturers are switching to providing their documents electronically: the lab staff logs into a WEB environment and after being identified by their login credentials will be pointed to an updated list of relevant documents. These documents are downloaded by the user and must undergo the above stated process of authorising and distribution.
While the manufacturers part in the game is almost available, it’s time to propose a manageable IT supported procedure to simplify the quality management (QM) manager’s life in the lab. The most crucial part of process automation is the availability of a primary document ID that must be unique over system boundaries. Assuming a manufacturer will deliver this ID with the downloadable document, it will be easy for the lab to track further changes and updates of this document more easily – a local version of this document becomes obsolete and could be automatically replaced by the QM software. Furthermore, the software will initialise the authorisation and distribution processes and finally the archiving of the obsolete version.
Although so far the process will deliver significant benefit to the laboratory, it is still affected by manually conducted steps: the user has to display any new document to map its content to a position in the laboratory’s document tree before importing it to the local system.
Consequently the next step for the manufacturer is to provide additional information on the document (document type e.g. a lot of information, affected analyser, test, lot-number etc.) in machine-readable form (metadata). After setting up a proper mapping the laboratory’s QM software would be able to determine the correct position of any document in the document tree and the task of the user is limited to the decision regarding whether the document should be included in the local document collection.
This will finally deliver an improved and automated process for receiving new and relevant documents for the lab. As stated, existing but updated documents will be imported directly and start the local control process. Any new document will be presented to the lab staff, together with its desired position in the tree, that they can finally decide what to do with it. This decision will be added automatically to the audit trail.
As leading manufacturers have just taken note of this idea, it is time for the QM supplier to create the infrastructure to facilitate the QM work of a laboratory.
PROFILE
Following his analytical chemistry studies at Bochum University, Germany, under Professors William S Sheldrick and Gerhard Bergmann, Dr Markus Neumann gained his doctorate for work on nuclear resonance spectroscopy. He held various roles with well-known laboratory information systems (LIS) manufacturers before, in 2006, establishing Dr Neumann & Kindler Ltd. & Co. KG. with Heiko Kindler, the firm’s Executive Director. Dr Neuman’s focus is on quality management and IT-strategies in the medical laboratory.
03.08.2013