Efficient processes in the Finnish hospital HUS
By Dr Janne Aaltonen, Director R&D, HUS Administration Building, Helsinki, Finland
The Hospital District of Helsinki and Uusimaa (HUS) is the biggest of 20 hospital districts in Finland. It provides specialised and university level health care services in and around city of Helsinki, with regional responsibility of 1.5 million people.
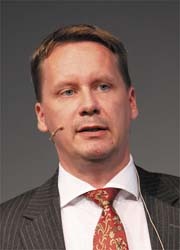
HUS has 23 hospitals, 21,000 employees (2,500 doctors), 1.4 million annual outpatient and 500,000 in-hospital visits, and annual revenues of 1.4 billion EUR. Helsinki University Hospital is part of HUS.
The HUS strategy was fully aligned in 2007. Our objective is to increase productivity 2–3% per annum, adoption of the purchaser/provider split, customer-orientated services and structures, and reform of operating models throughout the organisation. All of these objectives apart from purchaser/provider split call for process development. Actually, even before aligning the strategy the Ideal Hospital project was started, which aim is to develop a new process oriented concept for HUS.
The Finish healthcare system is relatively effective, if we use GDP proportion of healthcare costs as an indicator of efficiency. In 2005 Finland used 7.8% of GDP in healthcare (OECD health data). All people have access to public healthcare; there is also a small private sector (about 10% of services). Primary and secondary care is currently disintegrated, although there is a legislation process to join these two. Specialised care is provided by Hospital Districts, each municipality belong to one (of 20). Most districts use DRG reimbursement system.
The quality of Finnish healthcare systems is also quite high if we ask people who have used healthcare services. Finnish people regard our system third best in the EU (EurLIFE survey 2003). If we combine efficiency as a GDP share and quality as asked from people, we can find Finland the number one OECD country in quality-efficiency matrix. Low costs are mainly due to lower than average personnel cost because of smaller number of doctors and nurses.
We have described numerous processes in diagnosis or treatment level, for example hip replacement procedure, angioplasty, diabetes, etc. This is what we should do if we want to develop standard operating procedures for treatment of patient groups. However, there is a problem of high number of separate diagnoses and treatment options and in addition high variety between patients (acute vs. chronic, emergency vs. elective, etc.). Therefore we wanted to study if there are process steps and subprocesses common to different patient groups and specialities. And, naturally, there are. A referral process, diagnostic process, operation process or transfer process is similar between different patients and specialities.
By combining these two approaches we can form two-dimensional process matrix, elements that are common to all patients at certain stage (vertical process) and elements which are common to all patients at certain diagnosis or treatment (horizontal process).
If we consider all medical care, we can find out, that processes in emergency care and elective care are quite different. Elective care is scheduled; therefore we can utilise resources differently from emergency care. Also, an elective patient has a diagnosis, while first step of emergency care is to define diagnosis. Due to differences in these processes we have concluded, that it would be reasonable to separate elective care totally from emergency care. Similarly there are major process and resource optimisation differences concerning elective in-hospital treatment and elective ambulatory services where people flow anyway, i.e. in shopping centres and city centres, not in the hospital environment.
As a conclusion, there are two ways to define processes in hospital: 1) customer processes (vertical), which allow optimising allocative efficiency (‘doing right things’), and 2) production processes (horizontal), which allow optimising technical efficiency (‘doing things right’). Customer processes can be used in developing ICT, and for comparison of different specialties in one organisation. Production processes should be used to standardise operating procedures, and for comparison of one unit in time, and same activity in different organisations.
We expect productivity gain of 10–20% by standardising customer processes, and 5–10% by standardising production processes.
01.09.2008