Computers make prosthetic legs fit better
Report: Dot M McSherry, i.t. Communications
The fit of a prosthetic leg is a vital element in determining how well an amputee will function and adapt to the device. Historically, this has been a time-consuming art performed by skilled prosthetists. Today, computers have added science to the mix.
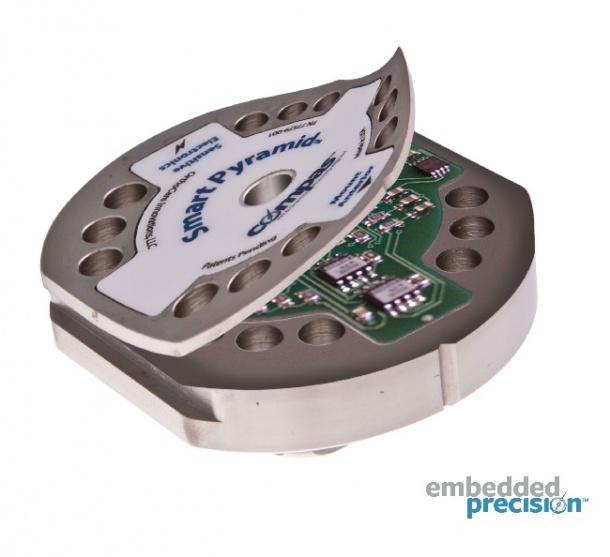
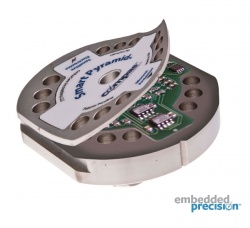
Prosthetic devices are not compatible with the physiology of the human body. Their limitations require regular adjust to accommodate for changes in an amputee's size and body volume, as well as changes in gait as they become more adept at using a prosthesis.
A real–time gait analysis system using a combination of hardware and software is one such innovation. The Computerised Prosthesis Alignment System – or Compas – consists of a device with embedded sensors that attaches to a prosthetic limb and measures gait, balance and other dynamic forces while an amputee is standing or walking on any type of terrain at any speed. It uses wireless technology to transmit this information to an automatic gait analysis software loaded on a personal computer.
The data is analysed, and a sophisticated computer model predicts whether a prosthetic device is misaligned, and if so, how it is misaligned. This is calculated through kinetic measurement analysis. The system shows the prosthetist precisely what is happening biomechanically, and recommendations are provided in easy-to-follow format. The prosthetist makes adjustments with a wrench.
The system’s hardware consists of a metal plate installed near the socket of the prosthesis (image 1) and a diagnostic module that attaches to it (photo 2). The plate has silicon strain gauges to measure various forces going through the prosthetic device and electronics and memory to enable this information to be converted into digital format and stored. When a patient visits a prosthetist to have adjustments made, the diagnostic module is attached to the plate. It projects a line on the floor or ground as a patient walks, and a gyroscope measures the rotation of the limb.
Compas technology is based on direct measurement of socket reactions, and uses a database of over seven million data points that measure exactly how socket reactions change with alignment alterations. The system is based on the theory that a prosthesis could be aligned in a consistent way if observed performance and sensations could be captured and measured while a patient was walking.
The company designing this technology is Orthocare Innovations, with offices in Oklahoma City, Oklahoma and Seattle, Washington. Founded in 2006, it developed the system with grant assistance from the U.S. National Institutes of Health and the U.S. National Centre for Medical Rehabilitation Research. When the product began to be commercially sold in 2009, Compas was named as one of the 100 most technologically significant products of the year by R & D Magazine.
Prosthetists have reported that the system makes the process of fitting a limb faster and easier for themselves and for the patient. However, expertise is still needed to achieve an optimum fit for a patient. It’s just that art of fit is now being combined with science.
21.05.2010