Ergonomic design in medical technology
It’s not just an industrial designer’s buzzword. This concept brings added value to patients, staff and manufacturers
Anja Behringer reports
The application of ergonomic principles can enhance product design and, more importantly, the usability of medical devices. Ideally the operation of the product is adaptable to the individual user’s preferences and to different workflows, for example when safe handling is ensured in routine as well as in emergency situations.
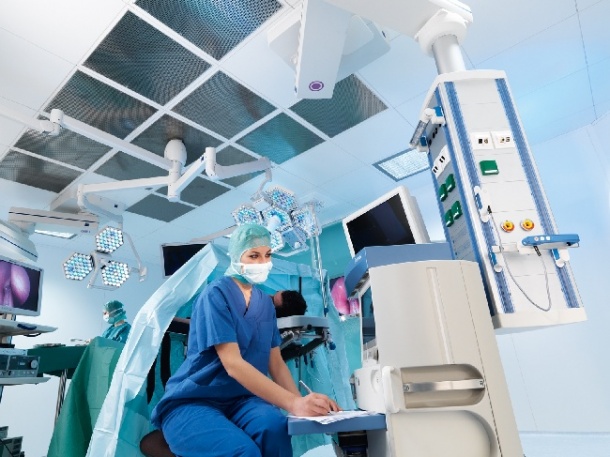
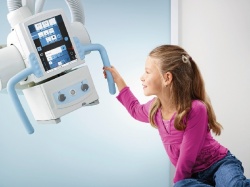
One of the objectives of ergonomic design is minimising user errors and thus patient safety since incidents and damages caused by user errors most frequently impact the patient. However, healthcare staff is also exposed to danger when a medical device is electrically operated, when it contains harmful substances or ionised radiation. While technical safety standards aim at managing these obvious risks, proper product design can help reduce many other risks that are frequently not considered outright dangerous, such as unhealthy posture, crush and puncture injuries or cuts.
Ergonomic design is still often considered a superfluous marketing gimmick that only drives up acquisition costs. A close look at the figures, however, tells a different story: Additional costs accumulated in the course of the useful life of a product often significantly exceed the price difference between the cheap and expensive product. Over time the ergonomically designed medical product is often less expensive than the product with the same technical features but a lower price tag.
Self-explanatory, easy and clear operation of a medical device creates more space for medical and nursing care. It reduces training times and increases user acceptance. If users feel comfortable working with a device the error rate will drop – another cost-saving factor. Whenever a job description is modified or expanded a review of the tasks and processes is recommended as well as their comparison to the original needs regarding workplace set-up. Test phases for new equipment are useful and taking a look at the sheer size of a user manual can be telling. For purposes of cost-benefit analyses the mandatory manufacturer’s notes on training requirements are also helpful.
Ergonomic design that saves time and costs has many more – seemingly mundane – aspects. Is the surface of the device dirt-resistant; the display easy to clean, and the colour selection appropriate for the product’s functions? Noise design can also be an important issue if, for example, equipment is used in intensive care units. Noise level and the alarm sound should be considered: a device should also have a unique sound to distinguish it from other devices.
Alarms with soft audio sequences offer better recognition than single shrill tones. In studies, the recognition rate of the single shrill sounds was below 50% and staff and patients felt extremely annoyed by loud and unpleasant noises.
In radiology and nuclear medicine, the conflict between the priorities image quality and radiation dose is a crucial issue. The higher the image quality, the higher is the dose. To ensure patient and operator safety, manufacturers and physicians alike follow the ALARA principle (As Low As Reasonably Achievable). For their radiology equipment that operates with X-rays or radioactive tracers Siemens, for example, developed several technologies – the so-called Combined Applications to Reduce Exposure (Care) – that allow a significant dose reduction while maintaining high image quality. The system issues a warning as soon as a certain dose threshold is reached. The examination reports can be analysed according to certain criteria and processes and workflows can be optimised -- another innovation that saves time and money.
25.02.2011