Automation: a five-year experience
Work procedures have been radically simplified since, over one weekend five years ago, two specialist laboratories owned by Dr Helge Riegel GmbH Medical Supply Centre in Wiesbaden, Germany, installed two Olympus OLA2500 systems.
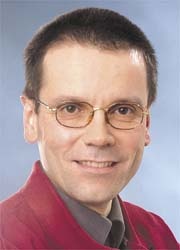
‘The goal was to have one system in routine operation by the Monday. However, we were actually able to put both to work immediately!’ exclaimed Dr Patrik Zickgraf, specialist at the Centre’s clinical laboratory.
The clinical medicine laboratory serves around 1,100 registered doctors and processes about 5,000 samples a day – roughly five million analytical tests each year.
‘The new laboratory electronic data processing system led to changes in our existing procedures, including the introduction of barcode labelling,’ Dr Zickgraf told us. ‘Our laboratory archives sample tubes for four weeks. Previously we would record the procedure and then divide the samples broadly by departments. Sub-division was performed manually with final distribution to different analytical workstations performed only after this stage. This distribution of samples in the specialist medical laboratory is very complex, resulting in the risk of sample mix up; confusion during accepting and distribution; difficulties in traceability and a high consumption of materials during sub-division. Since we have many workstations, the flow of samples around the laboratory was not optimised. This all highlighted our need for automation.
‘The OLA2500 was the only system that covered all our requirements – indeed it still does. It is straightforward and practical. Thanks to the automatic archiving we can now quickly locate samples, traceability is always ensured; we can document and trace the path of the sample from intake up to archiving. We have also reduced turnaround time (TAT) within the laboratory due to enhanced performance in distribution, processing and archiving.
‘Finally,’ he added, ‘we have experienced a significant reduction in serum consumption, since automatic sub-division takes only the volume that is actually required. The OLA systems have given us more time to ensure the quality of our analytical work and also enabled us to redeploy staff from distribution/archiving work to other more productive tasks.’
The Centre’s two machines are overseen by just one staff member. How has the equipment affected the lab teams? ‘Staff acceptance is high because the reliability and robustness of the OLA2500 systems is so immense; even if a very infrequent fault does stop the system, it can generally be rectified immediately by our experienced staff,’ Dr Zickgraf pointed out. ‘When the need arises, the excellent training of the Olympus service engineers has brought the machines back into service the very same day. The OLA2500 is a successful system; it’s made relaxed operation possible,’ he added.
‘We now have five years experience with laboratory automation, providing us with a very clear and transparent workflow. This transparency, and the fact that the laboratory staff can see for themselves the advantages that the system brings, generates acceptance. This also allows us to continually optimise our work procedures. Above all, it is essential that everyone understands the ‘‘path taken by the sample tube’’. Only then can they grasp the benefits delivered by automation.’
01.07.2008