Safer indoor air
Innovate Indoor Air Quality (IAQ) is a conceptual and operational development. It is
comprehensive, modern and multifaceted, to understand the risks and find solutions for indoor air. It goes beyond the sick building concept to define healthy environments and beyond the idea of indoor air being the only contaminant source.
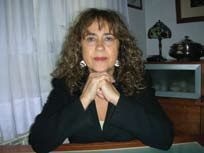
an expert technician in environmental indoor quality for ENAC (National Entity of Accreditation), and the founder and member of the Board of the Catalan Association of companies specialising in sick building syndrome. From 2001-2007 she was President of Spanish Federation Enterprises of Environmental Indoor Quality, and is currently Director of SEGLA, a firm specialising in the indoor environmental quality of buildings.
During a discussion with Dr Eduardo de la Sota, Dr Gloria Cruceta MD MBA explained its scope and value:
"IAQ means the absence of physical, chemical or biological contamination that could affect health or quality of life of patients or hospital staff, Dr Cruceta explained. ‘Using air quality control we may minimise or eliminate infections that could affect patients, basically via air, which are so prevalent in hospital settings. These infections are especially dangerous for inmuno-depressed patients, ending in severe health complications and sometimes death. Thus, environmental control in hospitals is a key issue concerning patient’s safety and healthcare quality. It obviously involves ethical considerations for the healthcare system.
Hospitals are to be differentiated in areas, according to the level of risk that patients present in each case; the higher the risk to air and environment, the higher the control that should be implemented. Special control should be undertaken for inmuno-depressed patients, neonatology and surgical areas.
To avoid airborne nosocomial infection, the operating theatre (OT) and adjacent areas of the surgical department have an exigent control of the air quality. Quality assurance requires verification of the correct functioning of all specific and complex installations in an OT, where biosafety is an essential condition.
The parameters to be controlled are:
• The relative pressures.
• The air conditioning parameters, temperature, RH, air changes, Validation of HEPA filters efficacy, configuration of air circulation.
• Room classification according to ISO 14644-1:
- OT Class A: Cardiac, orthopaedics, surgery, transplantation.
- OT Class B: Conventional surgery and emergencies.
- OR Class C: Ambulatory surgery and delivery rooms.
• The microbiological control will be required.
All of all these factors, along with personnel discipline, will bring the validation of quality conditions of the OT.
SEGLA is a consulting company that specialises in indoor quality, with extensive experience in the catering sector.
We follow the ISO requirements. ISO 14644-1 covers the classification of air cleanliness in clean rooms, OTs and other controlled environments. Classification of Air Quality (particle counting), according to ISO 14644-1, is a valuable tool that guides the human team involved in controlling nosocomial infection.
Our methodology is based on the determination of basic parameters that ensure the quality of air, for the prevention and control of infections transmitted by the hospital environment. We organise courses on indoor air quality in OTs and critical care areas. These are designed for specific training on the Prevention and Control of Nosocomial Infections and are particularly aimed at committees for hospital infection control, preventive medicine, managers and maintenance technicians, safety and risk assessment services, doctors and supervisors.
Besides these, interestingly the need to adapt to the Anti-smoking law (Spanish law) requires that premises with an area greater than 100 square metres, and in the case of permitting smoking, a properly marked, separate smoking area may not exceed 30% of the usable local area, or 300 square metres. Also, these dimensions should be physically separated by a fence, wall or glass, and a separate ventilation system.
Improvements
In Spain, there is an increasing improvement in all aspects involving management and control over environmental aspects concerning patients. Multidisciplinary teams have been created so that physicians, engineers, maintenance technicians and other professionals can work together and cope with all the possible variables to be considered. AENOR constantly provides information and normatives to reach the higher standards for the safety, health and quality of care in the healthcare industry.”
26.01.2010