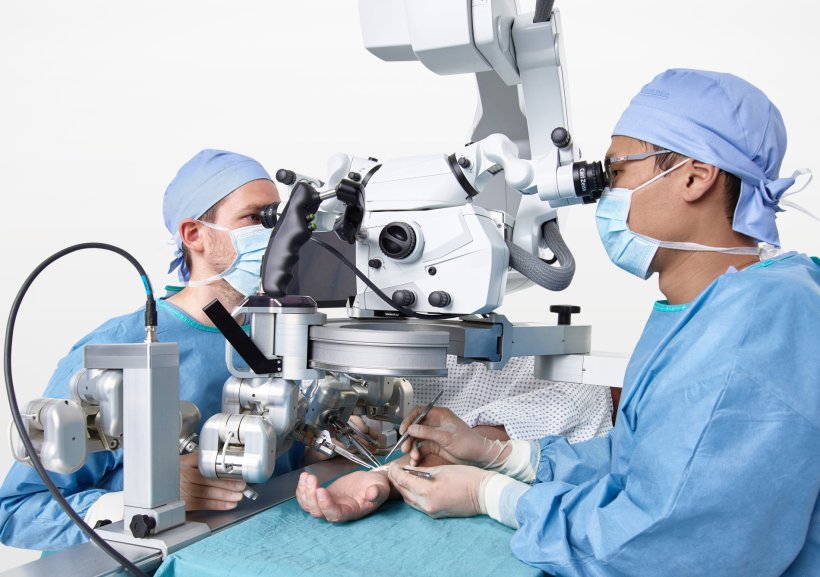
© Microsure
Article • State of the art and latest advances in technology
Robotic assistance in the operating theatre
Surgical robots are becoming widespread in operating theatres, delivering accuracy and safety. An overview of the main systems, principal operators, the market and European initiatives in this field.
Report: Bernard Banga
Modern surgery has come a long way in the past decades, thanks to improved techniques, tools and medical equipment. However, traditional surgery still has some limitations, including accuracy as well as fatigue and hand tremors in surgeons, which can impact the quality of procedures. For example, with spinal surgery, accuracy of movement must be better than 2 mm to avoid spinal cord injury. The threshold for errors is very low too, with a rate lower than 3% being necessary to avoid serious postoperative complications. In brain surgery, these margins become even smaller, with movement accuracy > 1 mm and error rates > 2%. Ophthalmic surgery takes this to the extreme, with an accuracy limit better than 0.5 mm to avoid corneal damage, and error rates less than 1%.
1.5 million robot-assisted procedures each year
These limitations have led to the emergence of robot-assisted surgery, which has dramatically increased the accuracy of surgical procedures while reducing hospitalisation times and postoperative complications. Surgical robots have been designed for use in a wide variety of surgical procedures across multiple fields, including cardiology, gynaecology, and urology.
The latter has seen an especially pronounced surge in robotic use; while in 2008, only 1.5% of urology surgery was performed with robot assistance, this has skyrocketed to over 43% today, according to various hospital sources. In total, some 1.5 million surgical procedures are performed worldwide using surgical robots. The advantages of this are manifold, including access to difficult areas through the use of slender, flexible robotic arms and on-board cameras, stable navigation of surgical instruments, significant reductions in operating times and hospital stays, as well as a reduction in postoperative complications (bleeding, infections, etc.). According to the colloquium paper “The state of the art of robotic surgery”, presented in October 2022 in Lyon, France, at the French Association of Biomedical Engineers congress, 71 technology options for automation and assistance with surgical gestures are currently available from 63 companies around the world.
The procedures that have benefited most from surgical robotics include prostate removal and renal ureter repair, gastrectomy, cholecystectomy and colectomy, plus heart valve surgery and coronary bypass surgery, along with total hip and knee replacements. This is a burgeoning market expected to be worth $14.9 billion by 2028.
Three robotic systems
The top five surgical robot manufacturers by market share in 2020 were Intuitive Surgical, Stryker, Medtronic, Zimmer Biomet, and Smith & Nephew. Intuitive Surgical supplies four robots for urology, ENT, abdominal and gynaecology surgery – the Da Vinci and Ion platforms. These have a market share of more than 69% between them. Stryker has the Malo platform, with a motorised arm holding cutting instruments (oscillating saw, acetabular burr) linked to an infrared stereoscopic system for partial knee replacement surgery. Medtronic has developed two systems: a semi-automatic navigation assistant named the Mazor X Stealth Station, for rectifying spinal deformity, and the Hugo RAS multi-port remote guidance system. Zimmer Biomet markets a semi-automatic navigation assistant for partial and total knee replacement, its Rosa Knee robot. Finally, Smith & Nephew has the Navio FPS platform, a manual navigation assistant using a handpiece combined with an optical navigation system designed for partial and total knee arthroplasty.
The process of choosing and introducing these high-tech systems into the complex environment of the hospital must be subject to a structured and complete methodological approach
Hervé Jacquemoud
Faced with the emergence of numerous surgical robots, the biomedical and equipment department at Geneva University Hospitals in Switzerland, together with the Swiss Foundation for Innovation and Training (SFITS), have just published a guide listing and classifying all automation and assistance technology options for surgical gestures. This collaborative effort is the result of a year-long survey of robots on the market. ‘The process of choosing and introducing these high-tech systems into the complex environment of the hospital must be subject to a structured and complete methodological approach,’ explains Hervé Jacquemoud. His team distinguishes between guidance assistants, laparoscopy devices and telesurgery systems. ‘Depending on whether the guidance assistants have a motorised arm, an instrument holder and whether they perform the procedure autonomously, we classify these into visualization assistants and manual, semi-automatic or automatic guidance assistants,’ the expert continues. Within the category of automatons, robots are sub-classified as motorised or non-motorised augmented instruments, or motorised endoscope holders. Finally, telesurgery systems are said to be single-port when only one incision is required, and multi-port for several.
Future generations of surgical robotics supported by the EU
The number of knee replacement procedures in OECD countries is expected to increase from 2.4 million procedures today to 5.7 million by 2030. ‘Currently, 95% of procedures are performed with no robotic assistance and with a very high patient dissatisfaction rate of more than 20%,’ observes Sophie Cahen, co-founder and CEO of Ganymed Robotics. Her med-tech company, based in Paris, France, has been selected by the EU for inclusion in a project which hopes to develop a compact robot to make joint replacement surgery more precise and less invasive. The initial focus is on total knee replacement, though Ganymed is looking to expand this to other joints including the shoulder, ankle and hip. This advanced robotics for optimised orthopaedic surgery project has been awarded a €3.5 million grant. Since its inception in 2018, the French startup has rapidly validated its proprietary algorithm based on pre- and intra-operative data collected via an observational study on 100 patients. ‘We aim to offer the first compact, ergonomic, intuitive and cost-effective robotic device,’ says Cahen. This next generation of robot introduces computer vision-driven intelligence and perception into the operating theatre, allowing contactless localisation of the patient’s anatomy and opening the way to data-driven operating theatres.
Microsure, based in Eindhoven, the Netherlands, is a spin-off from Eindhoven University of Technology (TU/e), and has developed the world’s first clinically available CE-marked microsurgery robot. The Meet MUSA project, funded by the EU to the tune of more than €2.6 million, will tackle the obstacles to successful product roll-out, including scaling up and optimising manufacture. Mechanics, electronics engineers, software developers and control engineers at Microsure have designed a system where surgeons look through 3D glasses at a large screen connected to a digital microscope positioned above the patient. The movements made by the surgeon using joysticks are detected and transformed into highly accurate movement of the small, lightweight robot attached to a platform fitted with arms able to hold and manipulate microsurgical instruments. In a 2020 study, surgeons reported using MUSA to treat breast cancer lymphoedema, a chronic condition that commonly occurs as a side effect of cancer treatment and is characterised by a swelling of body tissue as a result of a build-up of fluids. To perform the surgery, the robot sutures tiny lymph vessels measuring just 0.3 to 0.8 mm in diameter to nearby veins in the affected area. ‘Given this large unmet need in microsurgery, we are convinced that the time is right to launch MUSA on the market,’ said Sjaak Deckers, CEO of Microsure. The company will introduce MUSA across Europe by 2029, confident that that it will achieve major social and economic impact.
Five generations of surgical robots
- 1980 – neurosurgery. The first generation of surgical robots was developed for neurosurgery. The robot was used to position a probe in the brain with great precision. This first generation of robots were manufactured by AESOP Medical (US) and ZEUS Robotics (Canada). The AESOP robot was controlled by a remote surgeon, while the ZEUS robot had a more advanced interface, allowing the surgeon to control the robot’s movement.
- 1990 – remote control. The second generation of surgical robots saw the introduction of robotic laparoscopy surgery. The robot was able to control the surgical instruments remotely, allowing the surgeons greater precision and ease of use. The manufacturers of this generation of robots were Intuitive Surgical, Computer Motion, and SRI International, all from the US. The Intuitive Surgical robots were the most advanced, offering surgeons greater dexterity, accuracy, and stability.
- 2000 – more indications. The third generation of surgical robots was characterised by the extension of robotic surgery to include cardiac and orthopaedic surgery. Robots from this generation were more compact, easier to use and more precise than previously. The manufacturers here were Intuitive Surgical, MAKO Surgical, plus Mazor Robotics from Israel. Intuitive Surgical robots dominated the market with their advanced technology, high precision, and ease of use.
- 2010 – the limits of precision pushed back. The fourth generation of surgical robots saw the introduction of precision robotic surgery, with robots capable of even more precise movements and control of surgical instruments. The robots in this generation were also smaller and more portable than before. Manufacturers included Intuitive Surgical, TransEnterix and Verb Surgical, all from the US.
- 2020 – artificial intelligence enters the operating theatre. Surgical robots use artificial intelligence (AI) to improve the precision, speed, safety, and reliability of surgical operations. For instance, the French company Robocath has developed R One, a robotic system for assisting cardiac surgery which uses AI to learn a surgeon’s exact movements in order to optimise the pathways taken by surgical instruments.
27.06.2023