Is Lean right for your organisation?
By Maria Foster, Managing Director, Whitebridge Associates, Pittstown, NJ
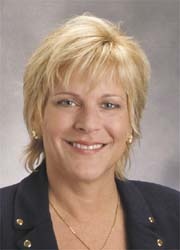
I have been involved in bringing Lean (and Six Sigma) methodologies to over 70 hospitals. In the early years, I was confident that Lean, with its proven results in industry, would drive significant improvements in healthcare delivery worldwide. However, I have found that while Lean is conceptually an amazing approach, it does not work in all hospitals. Not because some hospitals do not need Lean, but because some hospitals do not successfully implement and sustain a Lean culture.
What does it take to implement Lean?
The two most important components for a successful Lean implementation are strong leadership and breaking down the boundaries between departments.
The leadership of the hospital must be ready for the resource and time commitment needed to support a Lean implementation. Lean is not about tools or methods; it is a management philosophy and about creating a culture of continuous improvement. Organisations that are effective in implementing and sustaining Lean have leaders that:
- Create a vision
- Have an implementation plan
- Invest in in-house resources
-l Embrace change management
- Commit to staff education and coaching
- Monitor, quantify, and post results
- Motivate and reward employees for their contributions
Within each hospital there are a number of departments with different technologies, staff, and information flow. Often, these departments operate without knowledge of their impact on the rest of the organisation. Establishing a cross-functional team assists with viewing the movement of the patient as a continuous flow versus a series of individual steps.
It is often said that people change when they see the light or feel the fire. Hospitals that have successfully implemented Lean throughout their facility have started with a Lean implementation in a high risk area (e.g., medication delivery and management) or an area that incurs high costs or patient dissatisfaction (e.g., patient flow in an Emergency Department). These are areas where most employees agree improvements are necessary and where small changes can generate results quickly. Success in one area generates enthusiasm and becomes contagious throughout the facility.
What does it take to sustain Lean?
While a successful Lean implementation generates a lot of excitement, many facilities have found that the gains made start to dissipate over time, or remain isolated to a small area of the hospital system. Why does this happen? Again, it takes strong leadership and cross-functional teams committed to Lean to keep the momentum going. Without vigilance, people will go back to what they have always done.
Lean is a cultural and continuous improvement journey that never ends. Are you ready to start that journey? I recommend the use of an outside consultant to begin and then build your own competency. Be sure that the outside firm can communicate with your organisation. Work with someone who has taken the time to translate the Japanese concepts of Lean so that they are meaningful to your staff.
And, most of all, be committed for the long term to ensure an effective implementation and sustainable gains.
01.03.2008