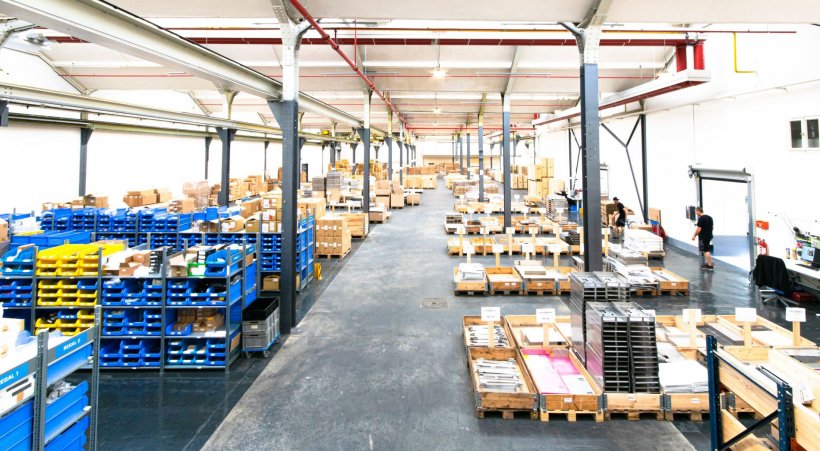
Image source: Rein Medical
Sponsored • Changing processes increased output by 30 percent
Streamlining and higher quality
Rein Medical, a leading supplier of customised all-in-one computer systems, high-resolution displays, customised OR wall modules and video and image management software solutions across Germany and Europe, produces high-quality, robust products. ‘To maintain these high standards going forward, the JVC subsidiary has enlarged and redesigned the warehouse and production area and optimised the processes,’ the company reports.
‘We are focusing on two separate production areas. The mechanical components are manufactured in the separate pre-production area, which keeps most of the dust and impurities outside the electronic assembly. In the production area, which is protected from electrostatic discharge (ESD) and air-conditioned, the assemblies are created on mobile workstations and then inserted into the pre-assembled housings. This protects the devices from uncontrolled electrostatic discharges, which can cause invisible damage inside the components.
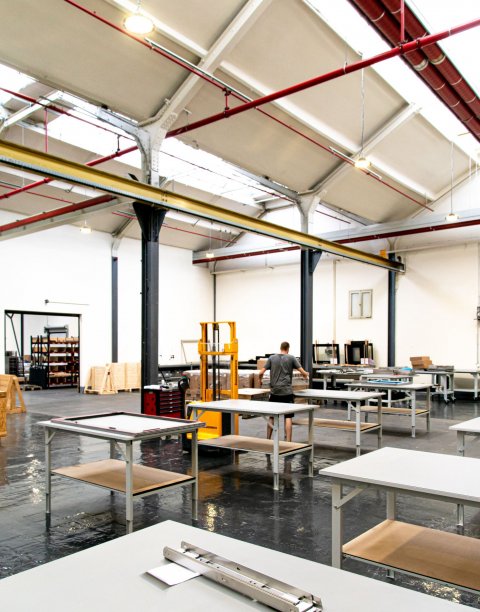
Image source: Rein Medical
‘Thanks to this more efficient production process and the enlargement of the production areas, we could increase production output by 30 percent, with less work for the production technicians and with the same number of production days. We have also improved quality assurance with the new ESD area,’ said Stephan Rein, founder and managing director of Rein Medical, when describing the new processes and their advantages.
During the redesign, special attention was paid to ergonomics at the workplace, he added. ‘After all, we want to create the best working conditions for our employees, and improve the quality of their work and products.’ The Mönchengladbach-based company benefited from the experience of its colleagues at JVCKenwood Corporation in Nagaoka (Japan) in regard to more efficient production and logistics processes.
Details: www.reinmedical.com
30.09.2021