Lean principles applied in path labs
Lean Laboratory and Lean Automation are vital ingredients for the efficient and productive running of today's modern pathology laboratories. Automation serves as an essential endorsement to Lean, says Paul M Button, Senior Consultant
at ValuMetrix, Ortho Clinical Diagnostics*
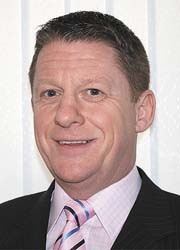
The underlying principle of Lean – to change the culture, create flow and eliminate waste in all its forms – is logical and readily understandable. It should be no surprise that Lean process improvement is the methodology of choice for the UK’s National Health Service (NHS). Considering its outcomes, it is clear that if Lean were a piece of equipment, every laboratory manager would buy one. But Lean is not a piece of equipment; it is a fundamental change in working practices and the thinking behind them. It is an attitude of mind, which constantly seeks to challenge and refine every aspect of working life. It is proven to work, but it can also hurt.
Established practices are demolished in the search for culture change, flow creation and waste elimination. Batch working and specialisation go out; single piece flow and cross training enter. Laboratory workers who are desperate for more space, discover they can work better with significantly less. Managers can discover the factors that really impact on their workflow; biochemists walk less as Lean processes improve laboratory layout.
Johnson & Johnson’s ValuMetrix Services group first made its Process Excellence methodologies, which include Lean, available to healthcare organisations in 1999. Its proven success is based on a training and mentoring model that recognises that culture change should not be imposed and that communications and commitment lie at the heart of any successful project. Unlike many consultancy or change management processes, ValuMetrix actually sets out to transfer intellectual capital and knowledge to the client organisation, so that future process improvement projects can be run from internal resources.
The majority of laboratories would benefit from automation, but this should not be incorporated until after lean implementation. Automating a non-Lean process will result in ‘automating waste’, which is very difficult to rectify. Achieving an efficient flow is usually impossible without some level of automation. The key is to achieve the right level. Too little means lost efficiency; too much means lost reliability and affordability.
ValuMetrix Services offer a combined Lean and Automation approach, whereby the initial phase ensures that the lab implements Lean principles followed by subsequent phases that implement automation at appropriate points in the operations. This is done by a Lean technique known as Value Stream Mapping, which moves the lab from the current state through a series of future states to achieve an ideal, world-class laboratory.
The results can be astronomical with substantial reductions in turn-around-times, substantial reductions in error, substantial cost savings and significant increases in productivity thereby allowing business growth without staff increase.
Further details can be obtained via your local Ortho Clinical Diagnostics office.
* A Johnson & Johnson Company
01.07.2008