Revolution
3-D printed muscles
With 3-D printing revolutionising manufacturing, its healthcare potential is being explored for medical devices, prosthetics, dentistry and drug development. One area under the spotlight is the creation of artificial muscles using a 3-D printing system. Dr Fergal Coulter, who has played an important role in helping develop the technique, outlined the manufacturing process, which he invented for his PhD, to create a system that could fabricate tubular artificial muscles.
Report: Mark Nicholls
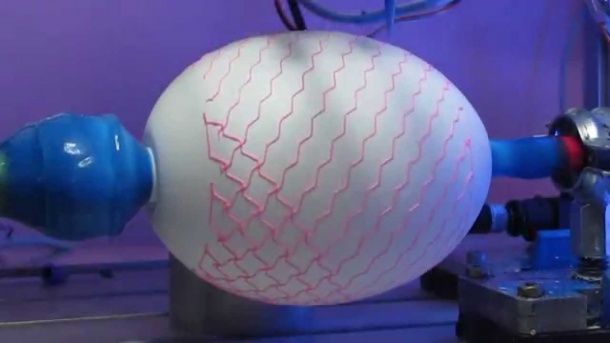
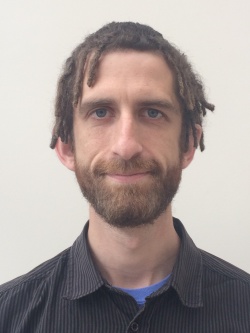
His focus was on Dielectric Elastomer Actuators (DEAs), which he proposes could be used potentially to create a fully implantable, electrically actuated, cardiac assist device.
Bio-robotic devices and prosthetics
Coulter, currently with University College Dublin and the Swiss Federal Institute of Technology in Zurich, said Dielectric Elastomers are a subclass of electro-active polymers, often referred to as ‘smart materials’ or ‘artificial muscles’. Whilst the technology is still evolving, there is hope that they can eventually be used within in-vivo bio-robotic devices and prosthetics.
The process to create the artificial muscle or cardiac device involves a 3-D printer capable of spraying multiple thin layers of silicone in a tubular fashion on to a rotating form, or mandrel. ‘These layers can be used as part of a solid state actuator, which when stimulated with a voltage will expand in area and, in doing so, act to pump blood – or any other fluid – in a peristaltic fashion,’ Coulter explained. ‘I designed the mandrel in such a way that compressed air can be passed through it from its central core to outer surface. Doing so has the effect of inflating the silicone layers, imparting a mechanical strain in the elastomer. This strain greatly improves the actuators’ efficiency and reliability.’
With a need to maintain some of the mechanical strain after the ‘balloon’ is deflated, he designed and built the printer so it could measure – via a 3-D scan - the shape of the inflated structure, then calculate and print the geometry required for the extrusion of a hard but collapsible support lattice around the outside of the balloon. ‘When the compressed air is removed, this structure somewhat constrains the actuator layers - holding them under a degree of tension,’ he said.
Soft, stretchable silicone layers
At EHI Live, in the live streamed session ‘4-D Printing of Inflated Structures for use in Dialectic Elastomer: Artificial Muscles?’ the 4-D printing aspect referred to the fact that the shape of the object changes during and after the course of being printed.
The technique involves soft, stretchable silicone layers being interleaved and separated by conductive electrodes. When these electrodes are charged, they are attracted to each other electromagnetically and the force generated has the effect of compressing the silicone in one axis, thus expanding it in the other two.
Coulter sees the potential for the 3-D artificial muscles to be used in a number of areas. ‘There’s good potential for these to see use as active prosthetic sphincters and oesophagus and cardiac assist devices, as well as in non-clinical applications, such as in soft robotics and in space.’ However, there is still more development work to be carried out before there is a clinical application.
The focus of his PhD, when at Nottingham Trent University (NTU), in England, was on the passive components of the device and design and building the 3-D printer itself. ‘Work is still needed in printing the conductive electrodes and control circuitry,’ he said, ‘along with testing and approval from regulatory bodies. But I have completed the first step in building what is a complicated and challenging device.’
NTU, with England’s National Health Service (NHS), has patented the concept with a view to further research and development. In the longer term, Dr Coulter foresees great benefits for patients. ‘As a pulsatile cardiac assist device, this could increase the mobility of patients who currently use a pneumatic aortic balloon pump, by removing the need for trans-cutaneous tubing, he explained. ‘In some cases, constant flow “total artificial hearts”, or indeed full surgical transplants, may not be needed. The primary purpose of the device is to increase the health of the existing heart by increasing the flow of oxygenated blood to the myocardium itself. Those suffering from oesophageal dysphagia or incontinence could also benefit.’
11.11.2015